
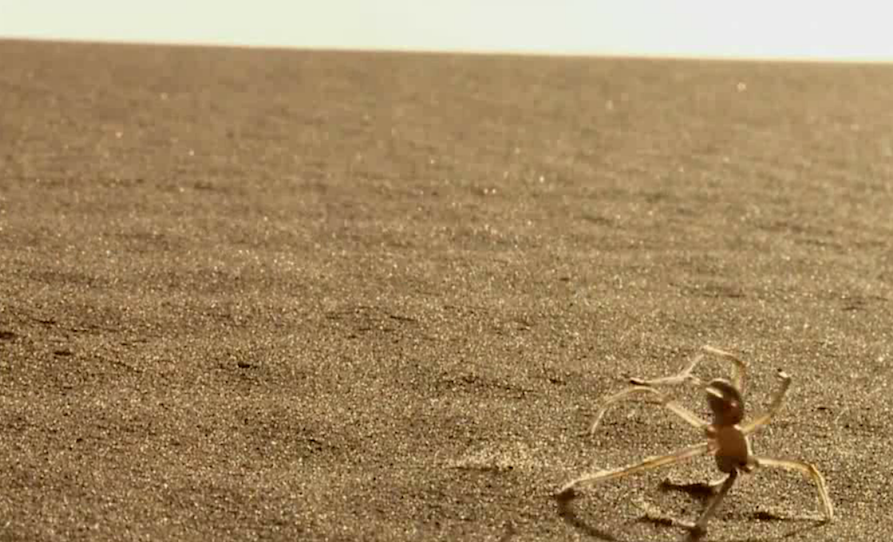
The whole workplace is ergonomically designed and can be adapted to people individually down to the lighting. At the same time, artificial intelligence and machine learning methods turn the BionicWorkplace into a learning and anticipative system that continuously optimises itself. In the BionicWorkplace, the bionic robot arm works together with numerous assistance systems and peripheral devices, which are networked and communicate with each other. The first is the BionicWorkplace, which integrates robots and a host of control devices and displays to help human users operate the system more effectively: It, too, is therefore much faster when rolling than walking and can even overcome inclines of up to five per cent uphill.įesto also made some more practical (if a bit less flashy) robotics announcements. Thanks to the integrated inertial sensor, it always knows what position it is in and when it has to push off again. In rolling mode, the BionicWheelBot does a somersault with its whole body, just like the real flic-flac spider. There are also 14 automatic-locking worm gear units that ensure that the spider only has to use energy when moving its legs-not, however, to keep its body upright when standing still. They are controlled by a total of 15 small motors, which fit in the knee joints and body. Like its biological model, the BionicWheelBot has eight legs, which help it to both walk and roll. As with the flying fox, the behavior of this robot is based very closely on the real thing: The guy in that video who both discovered the spider and invented the original robot ( Ingo Rechenberg, a bionics professor at TU Berlin) was also involved in the design of Festo’s version. The design is a little more creatively bio-inspired than the flying fox it’s based on the flic-flac spider, which lives in the Sahara and can move very quickly with a unique combination of cartwheel flips when it feels threatened:
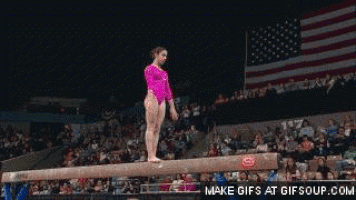
This means that the BionicFlyingFox can continue flying even if the fabric sustains minor damage.ĭiagram of Festo’s bionic flying fox, a type of megabat. The fabric’s honeycomb structure prevents small cracks in the flying membrane from getting bigger. Due to its elasticity, it stays almost uncreased, even when the wings are retracted. It consists of two airtight films and a knitted elastane fabric, which are welded together at approximately 45,000 points. The model’s flying membrane is wafer-thin and ultralight whilst also robust. Mimicking that required some creativity on Festo’s part:
Flic flac spider skin#
Flying foxes are the largest bats in the world, and as such, their wings consist of membranes of skin rather than feathers. Over the last few years, we’ve met ants, butterflies, flying jellyfish and penguins, kangaroos, seagulls, and much more.įesto has just announced its two newest bionic learning network robots-one is a very convincing flying fox, and the other is a walking, tumbling robot inspired by a Saharan spider.įesto calls their BionicFlyingFox an “ultra-lightweight flying object with intelligent kinematics.” It’s 87 centimeters long with a 228-cm wingspan, but it weighs only 580 grams. Which is good for them, and means they’ll keep making cool stuff. More often than not, it seems like Festo is able to take some of what it learns from designing and constructing these things and create practical new revenue-generating products. We love Festo because every year they invest an entirely appropriate amount of time and money into bio-inspired robots that are totally cool and very functional but have limited usefulness.
